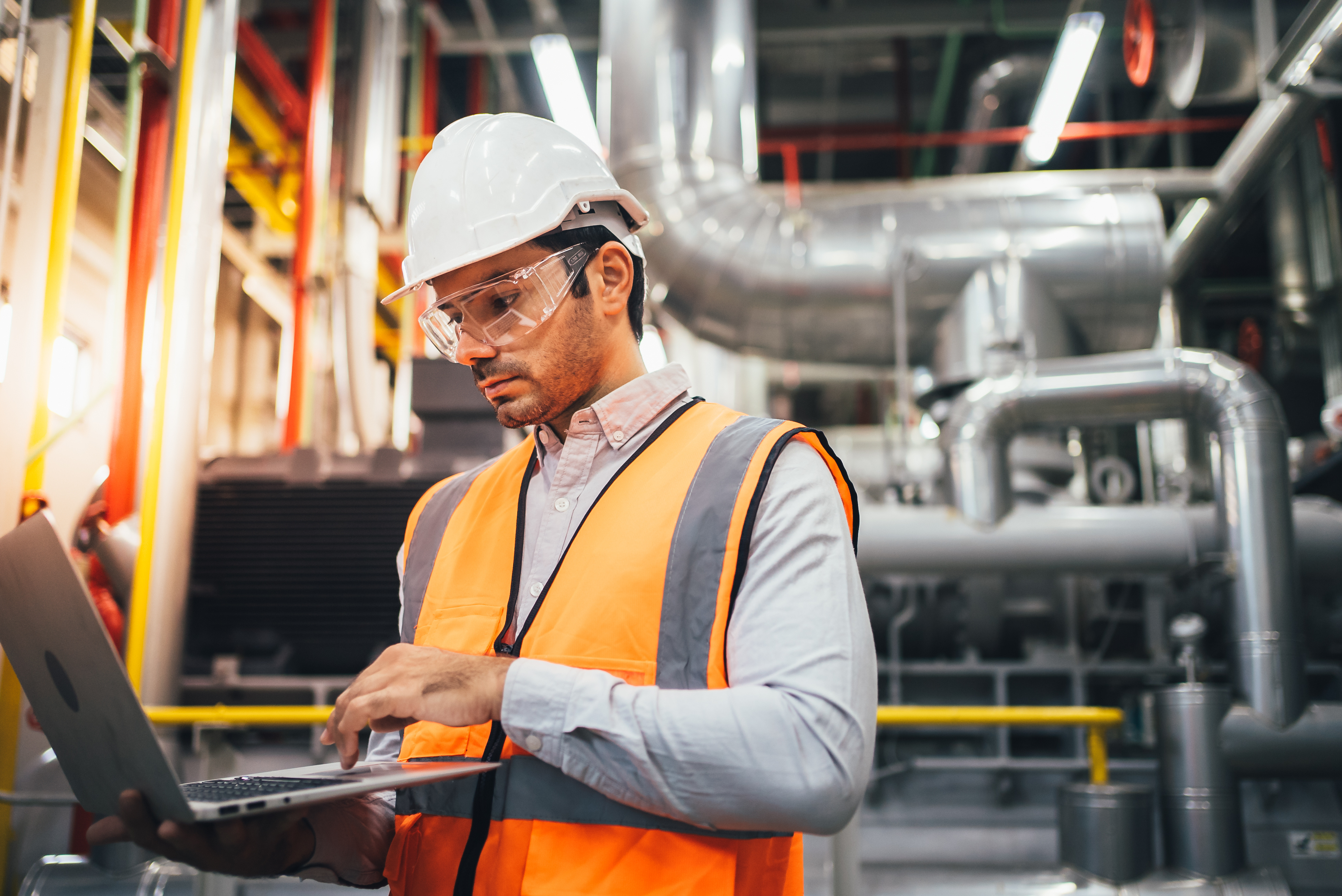
Understanding Predictive Maintenance
The Internet of Things (IoT) has introduced transformative predictive maintenance capabilities that help businesses monitor and analyze equipment performance in real-time, predict potential failures, and perform maintenance only when necessary.
Published on June 21, 2024
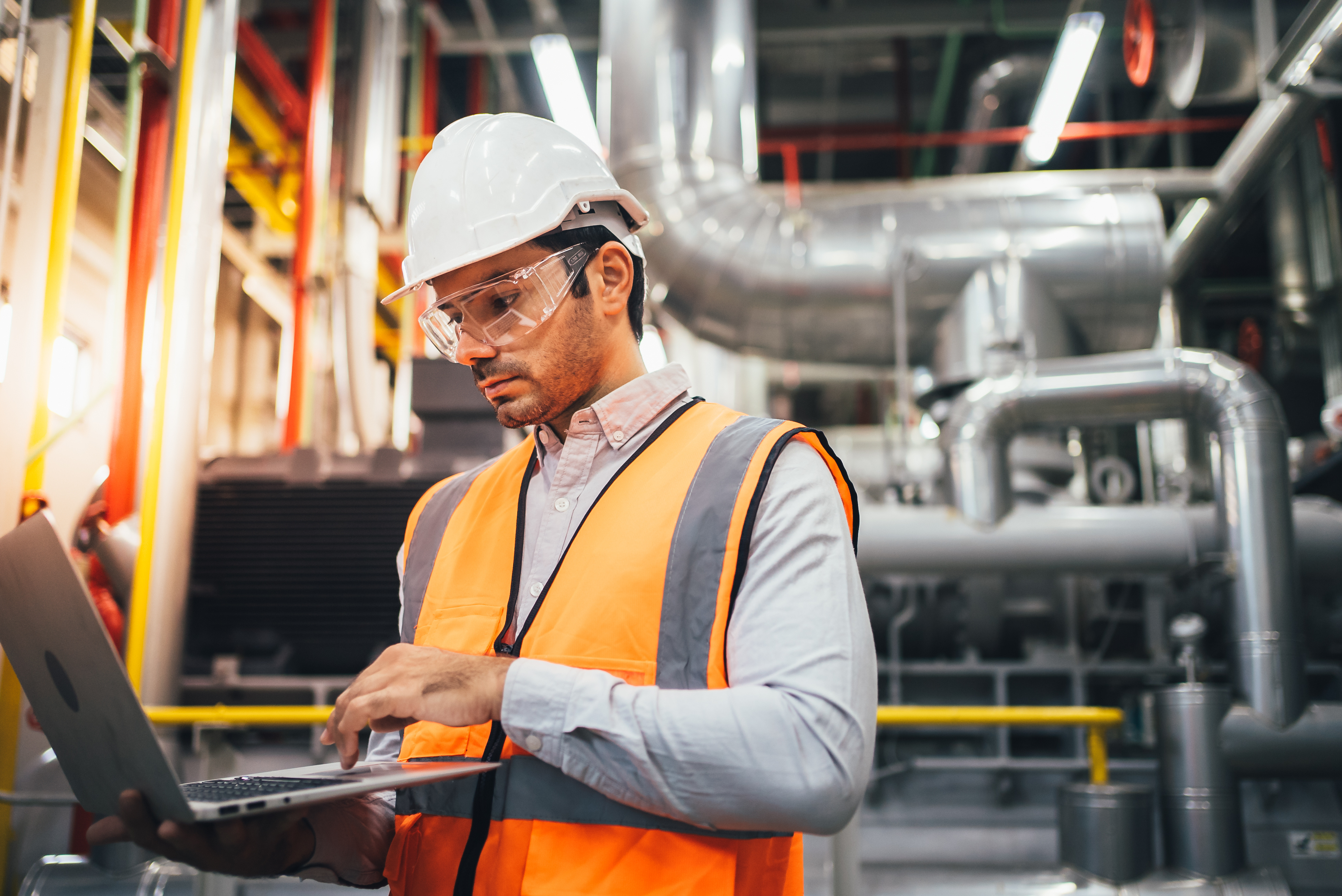
In today's industrial landscape where competition is at an all time high, maintaining the reliability and efficiency of equipment is more critical than ever. Equipment failure means extremely costly shutdowns and lost time incidents that can directly impact any business’ bottom line. The Internet of Things (IoT) has introduced transformative predictive maintenance capabilities that help businesses monitor and analyze equipment performance in real-time, predict potential failures, and perform maintenance only when necessary. This proactive approach not only means more efficient maintenance, but better maintenance strategies that reduce downtime and maintenance costs and extend the lifespan of equipment. In this blog post, we will explore the concept of IoT predictive maintenance, its numerous benefits, applications across various industries, challenges, future trends, and why it's an essential strategy for modern businesses aiming to stay ahead of the curve.
Introduction to IoT Predictive Maintenance
The Internet of Things (IoT) refers to the vast network of interconnected devices that communicate and exchange data with each other over the internet. These devices range from everyday household items like smart thermostats and refrigerators to complex industrial machinery and equipment. IoT technology enables real-time data collection, monitoring, and analysis, which can significantly enhance various operational processes, including maintenance strategies.
Traditional maintenance methods are often reactive (responding to equipment failures as they happen) or scheduled at regular intervals regardless of actual equipment condition. By contrast, predictive maintenance is a proactive approach that utilizes data and advanced analytics to predict when equipment failures might occur and to perform maintenance just in time to prevent these failures. Predictive maintenance aims to minimize downtime and extend the lifespan of equipment by addressing potential issues before they escalate into major problems.
With the integration of IoT technology, industries can predict equipment failure, reduce unexpected downtime, and optimize maintenance schedules. This creates tangible and significant cost savings, improved operational efficiency, and enhanced safety. This transformative approach not only boosts productivity but also provides a competitive edge in a rapidly evolving market.
Benefits of Predictive Maintenance
As previously mentioned, predictive maintenance offers substantial benefits across multiple dimensions, including cost savings, increased equipment lifespan, improved efficiency, and enhanced safety. By leveraging IoT technology, businesses can transform their maintenance strategies, achieving greater reliability and performance from their assets. The following is an overview of each of these improved outcomes.
Cost Savings
One of the most significant benefits of predictive maintenance is the reduction in unexpected downtime and repair costs. By using IoT technology to continuously monitor the condition of equipment, potential issues can be identified and addressed before they lead to costly breakdowns. This proactive approach helps avoid the financial impact of emergency repairs and the lost productivity associated with unscheduled downtime. Companies can allocate their maintenance budgets more effectively, focusing on preventative measures rather than expensive corrective actions. Whereas the old approach meant continuous box-checking, routine inspections, and an always-active approach to maintenance, predictive maintenance uses the information available via sensor data to make better use of repair personnel.
Increased Equipment Lifespan
Predictive maintenance extends the lifespan of equipment by ensuring that maintenance is performed only when necessary. Traditional maintenance schedules, based on fixed intervals, can lead to either over-maintenance or under-maintenance. Over-maintenance wastes parts resources and can cause unnecessary wear on components, while under-maintenance increases the risk of wear and damage leading to major failures. IoT-enabled predictive maintenance, on the other hand, allows for timely interventions that keep equipment running smoothly and efficiently, thereby maximizing its useful life without waste.
Improved Efficiency
Optimizing maintenance schedules and resource allocation is another key advantage of predictive maintenance. With real-time data and advanced analytics, maintenance teams can prioritize tasks based on the actual condition of equipment rather than relying on arbitrary schedules. This results in more efficient use of manpower, materials, and time. Moreover, the ability to predict and plan for maintenance activities minimizes disruptions to operations, leading to improved overall productivity and efficiency.
Safety
Safety is paramount in any industrial setting, and predictive maintenance plays a crucial role in preventing hazardous equipment failures. By identifying potential issues early, companies can mitigate the risk of accidents that could endanger workers and cause significant damage to facilities. Predictive maintenance ensures that equipment operates within safe parameters, reducing the likelihood of catastrophic failures. This not only protects the workforce but also helps companies comply with safety regulations and avoid costly liabilities.
It’s important to note that machinery is often showing signs of potential failure much earlier than can be detected by human inspection. Subtle patterns such as atypical vibration, sounds that are inaudible to the human ear, or fluctuations in temperature might spell out failure that an inspector would not notice – but that an algorithm can detect. In this way, machine learning approaches to maintenance can identify safety risks much earlier than is possible with traditional methods.
How IoT Technology Enables Predictive Maintenance
IoT technology empowers predictive maintenance through advanced sensors, sophisticated data analytics, real-time monitoring, and cloud computing. These components work together to provide a powerful, data-driven approach to maintenance that enhances reliability, reduces costs, and extends the lifespan of industrial equipment. By leveraging these technologies, businesses can transition from reactive to proactive maintenance strategies, achieving significant operational improvements and competitive advantages.
Sensors and Data Collection
At the heart of IoT predictive maintenance are the sensors that collect vital data from equipment. These sensors come in various types, each designed to measure specific parameters critical to assessing the health of machinery. Common sensors include:
- Vibration Sensors: Monitor the vibration levels of rotating machinery to detect imbalances or misalignments.
- Temperature Sensors: Track temperature changes that may indicate overheating or component wear.
- Pressure Sensors: Measure fluid and gas pressures to ensure they remain within safe operating ranges.
- Humidity Sensors: Monitor moisture levels to prevent corrosion and other moisture-related damage.
- Acoustic Sensors: Capture sound waves to detect anomalies such as leaks or mechanical faults.
These sensors continuously collect data, providing a comprehensive picture of the equipment’s operating conditions.
Data Analytics
Once data is collected, the role of big data and machine learning comes into play. Predictive maintenance relies heavily on data analytics to transform raw sensor data into actionable insights. Big data techniques enable the processing of vast amounts of information, identifying patterns and trends that would be impossible to detect manually. Machine learning algorithms analyze this data to predict potential failures and determine the optimal times for maintenance. By learning from historical data and continuously improving their accuracy, these algorithms provide increasingly reliable predictions, helping to prevent unexpected breakdowns and extend equipment life.
Real-time Monitoring
IoT technology enables real-time monitoring, a critical component of effective predictive maintenance. Continuous monitoring means that data from sensors is constantly being collected and analyzed, allowing for immediate feedback loops. This real-time insight ensures that any deviations from normal operating conditions are quickly detected and addressed before they escalate into major issues. Real-time monitoring helps maintenance teams respond promptly to emerging problems, reducing downtime and maintaining optimal operational efficiency.
Cloud Computing
The vast amounts of data generated by IoT sensors require robust storage and processing capabilities, which is where cloud computing comes in. Cloud platforms provide the necessary infrastructure to store large volumes of data and perform complex analyses without the need for extensive on-site hardware. Cloud computing offers scalability, allowing businesses to easily manage increasing data loads as they expand their IoT networks. Additionally, cloud-based solutions facilitate remote access to data and analytics tools, enabling maintenance teams to monitor and manage equipment from anywhere, improving flexibility and responsiveness.
Industry Applications
IoT predictive maintenance has wide-ranging applications across various industries, from manufacturing and energy to transportation and healthcare. By leveraging IoT technology, these sectors can achieve significant improvements in equipment reliability, operational efficiency, and cost savings. Predictive maintenance represents a transformative approach that enables businesses to move from reactive to proactive maintenance strategies, ensuring continuous operation and gaining a competitive edge in their respective markets.
Cloud solutions, like our Canvas™ Software Suite, make it easy to deploy, monitor, and update your IoT Devices wherever they operate. Canvas Software Suite enables rapid embedded development across our MCU-based wireless products. Cross-chipset middleware, easy-to-use wireless APIs, on-module scripting and intuitive desktop/mobile tools are all available to dramatically ease embedded development. Support is included for Iot Devices like our MG100 cellular gateway, our BT510 Bluetooth LE Multisensor, or our Sentrius BT610 Sensor. It’s also available on a selection of our wireless modules, like our Sera NX040 UWB module, Pinnacle 100 cellular module, Lyra 24 / BL5340 / BL654 BLE modules, and our BL654 pluggable USB adapter.
Manufacturing
In the manufacturing sector, IoT predictive maintenance is revolutionizing how companies monitor machinery and equipment to prevent production halts. Manufacturing facilities often rely on complex and expensive machinery that, if it fails, can lead to significant downtime and financial loss. By deploying IoT sensors on critical equipment, manufacturers can continuously monitor performance indicators such as vibration, temperature, and pressure (these are all supported via external probes on our BT610 sensor). Predictive analytics can then identify signs of wear and potential failures before they occur, allowing maintenance teams to address issues proactively. This not only minimizes unexpected downtime but also optimizes the scheduling of maintenance activities to avoid disrupting production schedules.
Energy
The energy sector benefits immensely from IoT predictive maintenance, particularly in the management of wind turbines, solar panels, and power plants. These energy systems are often located in remote or harsh environments, making manual inspections and maintenance challenging and costly. IoT sensors can monitor various parameters, including rotational speed, blade condition, and energy output in wind turbines, or temperature and electrical output in solar panels. By analyzing this data, energy companies can predict and prevent failures, ensuring consistent energy production and reducing maintenance costs. Additionally, predictive maintenance helps extend the lifespan of these renewable energy assets, contributing to more sustainable energy generation.
Transportation
In the transportation industry, IoT predictive maintenance enhances fleet management and the upkeep of vehicles and infrastructure. For fleet operators, maintaining a large number of vehicles involves significant logistical challenges and costs. IoT sensors installed on vehicles can monitor engine performance, tire pressure, brake conditions, and more. This data enables fleet managers to predict and schedule maintenance activities before issues lead to breakdowns on the road. Moreover, predictive maintenance can be applied to transportation infrastructure, such as bridges and railways, by monitoring structural health and detecting early signs of wear or damage. This proactive approach ensures safety, reduces downtime, and lowers the overall cost of maintenance.
Healthcare
The healthcare industry relies on the optimal functioning of critical medical equipment to provide high-quality patient care. IoT predictive maintenance is instrumental in ensuring the reliability and availability of devices such as MRI machines, ventilators, and diagnostic tools. Sensors embedded in medical equipment can track performance metrics like usage rates, temperature, and operational status. By analyzing this data, healthcare facilities can predict when equipment is likely to fail and perform maintenance at convenient times, avoiding disruptions in patient care. Predictive maintenance not only enhances the reliability of medical devices but also supports regulatory compliance and improves the overall efficiency of healthcare operations.
Challenges and Considerations
While IoT predictive maintenance offers numerous benefits, it also presents several challenges and considerations. Ensuring data security, integrating with existing systems, managing the initial investment, and handling large volumes of data are critical factors that organizations must address. By carefully planning and addressing these challenges, businesses can successfully implement IoT predictive maintenance solutions and reap the significant advantages they offer in terms of efficiency, cost savings, and operational reliability.
Data Security
One of the biggest challenges in implementing IoT predictive maintenance is ensuring data security. The vast amount of data collected by IoT sensors can be a lucrative target for cyber threats. Unauthorized access to sensitive information or malicious attacks on the network can lead to significant disruptions and data breaches. Therefore, it is crucial to implement robust cybersecurity measures. This includes encryption, secure communication protocols, regular security audits, and strict access controls. Ensuring that data is securely transmitted and stored helps protect against cyber threats and maintains the integrity and confidentiality of the information collected.
Our Summit Suite Security is one offering designed with all of these critical considerations in mind. Supported on our Summit SOM 8M Plus, 60 SOM, and IG60, the Summit Suite goes beyond the industry standard for ultra critical safety demands. Our Chain of Trust device security handles signed images, protected user space, device encryption, and secure key storage. We provide comprehensive CVE scanning to keep customers ahead of vulnerabilities in their complete software BOM. And we provide validated FIPS 140-2 Level 1 cryptographic modules for the most security-sensitive applications, like those required in government hospitals.
Integration with Existing Systems
Integrating IoT predictive maintenance solutions with existing systems can be complex, particularly when dealing with legacy equipment and infrastructure. Many organizations have long-established systems that were not originally designed to interface with modern IoT technology. Achieving seamless integration requires thorough planning and potentially significant modifications to current processes and equipment. Compatibility issues can arise, necessitating custom solutions or middleware to bridge the gap between old and new technologies. Additionally, staff may need training to effectively manage and operate the integrated systems. Overcoming these challenges is essential to fully realize the benefits of predictive maintenance.
Initial Investment
Setting up an IoT infrastructure for predictive maintenance involves substantial initial investment. Costs can include purchasing and installing sensors, upgrading network capabilities, and acquiring data analytics software. There may also be expenses related to integrating new systems with existing infrastructure and training personnel to use the new technology effectively. While the long-term benefits of predictive maintenance, such as reduced downtime and maintenance costs, can offset these initial expenditures, the upfront financial commitment can be a barrier for some organizations. Careful financial planning and a clear understanding of the return on investment are necessary to justify and manage these initial costs.
Data Management
Handling and analyzing the large volumes of data generated by IoT devices is another significant consideration. The sheer amount of information can be overwhelming, requiring advanced data management strategies and tools. Efficient data storage solutions, such as cloud computing, are essential to manage the scale and ensure data is accessible and actionable. Furthermore, sophisticated data analytics capabilities are needed to process and interpret the data in real-time, providing valuable insights for predictive maintenance. Organizations must invest in both the hardware and software necessary for effective data management, as well as in skilled personnel who can interpret and act on the data collected.
As we’ll discuss later, edge computing is one way to minimize the massive volume of data that currently rests on a central server’s shoulders. Microcontrollers or System on Modules, like our line of SMARC SOMs, can perform data collection and processing right on the device, passing along only the evaluation of that data and minimizing the processing needed at the central network. The more data collected and the more resource-intensive the processing, the more powerful a device needs to be. We offer a wide range of computing capability in our system-on-modules for all variety of application requirements.
Future Trends in IoT Predictive Maintenance
The future of IoT predictive maintenance looks promising, driven by advancements in AI and machine learning, the adoption of edge computing, the integration of blockchain technology, and increased industry adoption. These trends will enhance the accuracy, responsiveness, security, and widespread implementation of predictive maintenance solutions, leading to more efficient and reliable operations across various sectors. Embracing these innovations will enable businesses to stay ahead of the curve, leveraging cutting-edge technology to optimize their maintenance strategies and achieve significant competitive advantages.
Advancements in AI and Machine Learning
The future of IoT predictive maintenance is set to be profoundly influenced by advancements in artificial intelligence (AI) and machine learning. These technologies are continually evolving, enabling more accurate and sophisticated predictive models. AI and machine learning algorithms can analyze vast datasets, identifying intricate patterns and correlations that humans might overlook. As these technologies advance, their predictive accuracy will improve, leading to even more precise maintenance schedules and earlier detection of potential failures. This will further reduce downtime and maintenance costs, enhancing the overall efficiency and reliability of industrial operations.
Edge Computing
Edge computing is poised to play a crucial role in the evolution of IoT predictive maintenance. This technology involves processing data closer to the source—at the "edge" of the network—rather than relying solely on centralized cloud servers. By reducing the latency associated with data transmission, edge computing allows for faster decision-making and real-time responses. This is particularly beneficial for predictive maintenance, where timely interventions can prevent equipment failures and minimize disruptions. As edge computing technology matures, it will enable more efficient and responsive maintenance strategies, enhancing the effectiveness of IoT solutions. As previously discussed, system-on-modules provide a powerful platform for edge computing, with a wide array of device peripherals that can serve as the platform for an entire IoT device.
Blockchain Technology
Blockchain technology is emerging as a powerful tool for enhancing data security and integrity in IoT predictive maintenance. Blockchain’s decentralized and immutable ledger system ensures that data collected from IoT devices is tamper-proof and securely recorded. This enhances trust in the data’s accuracy and reliability, which is crucial for predictive maintenance applications. By providing a transparent and secure method for data management, blockchain can help mitigate concerns related to data breaches and unauthorized access. As industries increasingly adopt blockchain technology, it will further strengthen the security framework of IoT predictive maintenance systems.
Increased Adoption
As the benefits of IoT predictive maintenance become more widely recognized, its adoption is expected to grow across various industries. More businesses are realizing the value of predictive maintenance in reducing costs, improving operational efficiency, and extending the lifespan of their assets. The technology’s proven effectiveness in early adopters, such as manufacturing, energy, transportation, and healthcare, is encouraging other sectors to explore its potential. As a result, we can expect to see a broader implementation of IoT predictive maintenance solutions, driving innovation and setting new standards in maintenance practices across different industries.
Final Thoughts On IoT Predictive Maintenance
In conclusion, IoT predictive maintenance is revolutionizing the way industries manage and maintain their equipment. By leveraging advanced sensors, data analytics, real-time monitoring, and cloud computing, businesses can transition from reactive to proactive maintenance strategies. The benefits are substantial: significant cost savings, extended equipment lifespan, improved operational efficiency, and enhanced safety.
Predictive maintenance powered by IoT technology offers a comprehensive solution to minimize unexpected downtime, optimize maintenance schedules, and ensure the smooth and reliable operation of critical assets. As advancements in AI, machine learning, edge computing, and blockchain technology continue to evolve, the capabilities and effectiveness of predictive maintenance will only improve.
We encourage you to consider implementing IoT solutions for your maintenance needs. The transition to predictive maintenance can provide a competitive edge, improve your bottom line, and ensure the longevity and reliability of your equipment. As a premium connectivity partner, our line of hardware and software offerings represent a path into the IoT for new and legacy devices, leveraging popular technologies like Wi-Fi, Bluetooth, UWB, Cellular, LoRaWAN and more.
If you are interested in exploring how IoT predictive maintenance can benefit your organization, please contact us for a demo, consultation, or more information. Our team of experts is ready to help you harness the power of IoT to transform your maintenance strategies and achieve operational excellence.