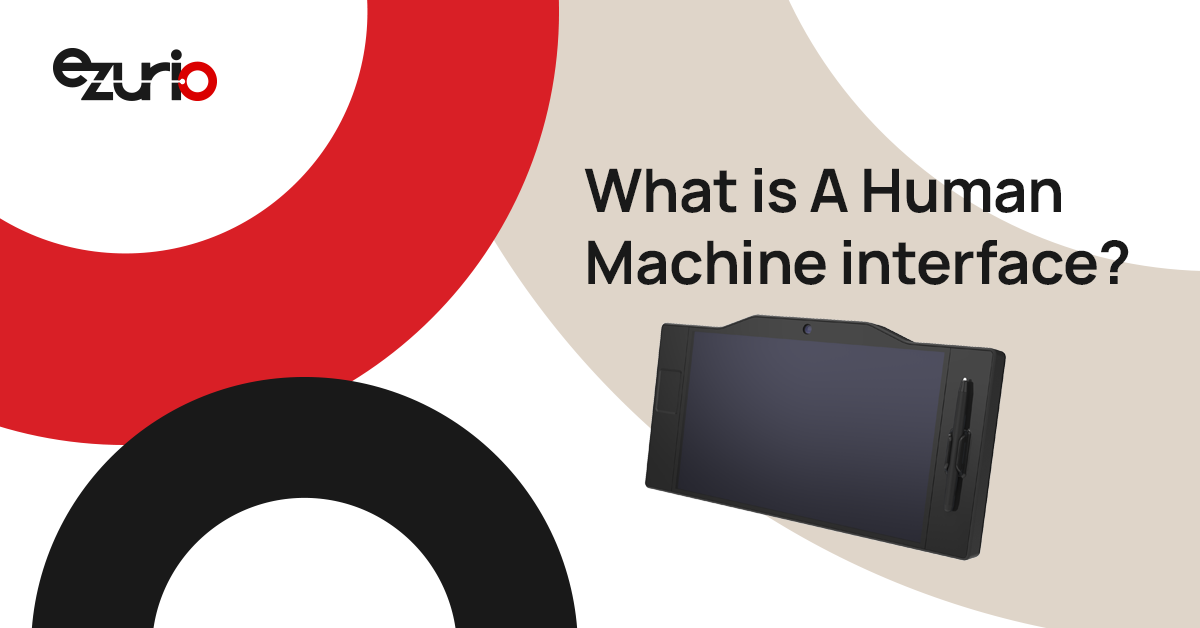
Functionality as a Bridge
HMIs serve as the crucial bridge in industrial environments, facilitating intuitive interaction with machines. Their primary function is to translate complex machine data into accessible information, allowing operators to monitor, control, and adjust processes in real-time. Here’s an expanded look at how HMIs function as a bridge:
- Data Translation and Visualization: Real-Time Monitoring displays data from sensors, showing equipment status instantly.
- Control and Interaction: Input mechanisms enable immediate adjustments to maintain optimal performance and reduce downtime.
- Enhancing Safety and Efficiency: User-friendly interfaces help reduce errors and support remote access for continuous operations.
Types of HMI
Industrial HMIs come in various forms, including:
Standalone Terminals: These are complete units with dedicated hardware and software, used in specific locations within industrial settings, such as control rooms or operator stations. They are designed for easy installation and often feature robust exteriors to withstand harsh environments.
- Use case: These terminals are ideal for applications that require dedicated monitoring and control points, such as power generation facilities where operators monitor and control turbines, boilers, and other equipment from one central location. Factory floors in manufacturing plants use standalone terminals to display real-time production data for assembly lines.
Embedded Panels: Integrated directly into machinery, these panels save space and are engineered for robustness and longevity.
- Use case: CNC machines in metalworking shops use embedded panels where operators input machining parameters and monitor cutting operations. Also, food processing plants use these panels in packaging machines to monitor the packaging process.
Mobile Devices: With the rise of mobile technology, HMIs have also transitioned into mobile formats, offering flexibility and remote access capabilities. These mobile HMIs provide flexibility and enable remote access to industrial processes.
- Use case: Oil refineries technicians use mobile HMIs to track inventory, manage stock, and coordinate shipping/receiving operations. Mobile HMIs are also frequently used in warehouses for logistics and inventory management.
Common Uses of Industrial HMIs
Industrial HMIs play a vital role in various applications, enhancing the efficiency, safety, and productivity of industrial operations.
Here are some common uses:
Monitoring and Controlling Processes
At the core of HMI functionality is the ability to monitor and control the machinery. This includes managing production lines, supervising robotic systems, and adjusting operational parameters to enhance efficiency.
Example: Manufacturing Plant
- HMIs are used to monitor and control robotic arms that perform welding, painting, and assembly tasks. Operators can adjust speed, sequence, and parameters of the robots.
Visualizing Data
HMIs are instrumental in visualizing real-time data, which helps in making informed decisions. This includes displaying metrics such as production timelines, system statuses, and operational outputs, which are essential for maintaining the efficiency of industrial processes.
Example: Food and Beverage Plant
- HMIs display real-time data on production metrics such as batch times, ingredient weights, and machine status. This visualization helps operators ensure that products meet quality standards and production schedules are on-time.
Interaction Enhancements
Modern HMIs incorporate touchscreens and other interactive technologies to provide immediate control and feedback, making them indispensable in today's automated and fast-paced industrial environments.
Example: Warehouse Fulfillment Center
- Interactive HMIs assist workers in managing packing and shipping tasks. Touchscreen interfaces allow quick entry of shipping information, scanning of barcodes, and tracking of package statuses, streamlining the entire packing process.
Current Trends in HMI Technology
Integration of Artificial Intelligence (AI)
AI is revolutionizing HMIs by making them more adaptive and intuitive. This technology enables HMIs to predict operator needs and automate responses, significantly enhancing operational efficiency.
In predictive maintenance, AI-driven HMIs can analyze historical data and current machine conditions to predict when maintenance is needed, reducing downtime, and preventing costly failures. For instance, an AI-enabled HMI might alert operators to a potential bearing failure in a production line robot before it happens.
Natural Language Processing (NLP) and Gesture-Based Inputs
The integration of NLP and gesture-based technologies in HMIs is making interactions more natural and efficient. This trend is particularly beneficial in complex industrial settings where speed and ease of use are crucial.
With NLP, operators can control machinery using voice commands, which is particularly useful in hands-free environments. For example, in a chemical processing plant, an operator can verbally instruct the HMI to adjust temperature settings or start/stop equipment. Especially helpful in clean-room application to reduce contamination caused by touching surfaces.
Blind HMIs
The concept of 'blind HMIs' involves controlling devices via mobile apps without the need for traditional display panels. This approach leverages the ubiquity of smartphones, reducing hardware costs and increasing accessibility.
Blind HMIs enable remote monitoring, allowing operators to oversee operations from any location. For example, in an oil and gas facility, engineers can monitor pipeline pressure and flow rates from their mobile devices, making real-time adjustments as needed without being on-site.
These current trends in HMI technology are driving significant advancements in industrial automation, enhancing efficiency, usability, and flexibility across many sectors.
The Future of HMIs in Industrial Applications
Predictive Analytics and Machine Learning
Future developments in HMI technology are likely to harness predictive analytics and machine learning, enabling proactive system management and anomaly detection before they impact production.
IoT Enhancements
The integration of the Internet of Things (IoT) is set to expand the capabilities of HMIs further, connecting them across devices and systems, thus enhancing the overall functionality and efficiency of industrial operations.
The IoT will help HMIs connect with a wide range of sensors and devices, providing a complete view on the entire operation. In a smart building, an HMI could integrate data from HVAC systems, lighting controls, security cameras, and occupancy sensors, offering comprehensive monitoring and control from a single interface. It can also optimize energy consumption by adjusting lighting and temperature based on occupancy and weather conditions, improving energy efficiency.
Customization and Scalability
As industries continue to evolve, the ability to customize and scale HMIs will become crucial. This adaptability will allow HMIs to meet specific operational needs, accommodating various industrial applications.
Future HMIs will offer highly customizable interfaces that can be tailored to specific workflows and user preferences. In a smart building, facilities managers might need a low resolution, simple HMI whereas a smart factory industrial plant may need higher computational power to perform analytics. Ezurio's Industrial HMI offers a range of processors (from the high-end to the value-conscious) that are configurabile to your desired application.
